1906
Company formation of a commercial enterprise by M. Franz Dvorak in 1010 Vienna
Specialization in metal deformed parts
1932
Take over by Mr. Johann Dvorak, born 1891
1950
Production changeover to punching and turning technology
1962
Take over by Mr. Johann Dvorak born 1927
1970
Moved from Vienna to Wolkersdorf – Lower Austria
Land area: 10 000 m², production area: 3 000 m²
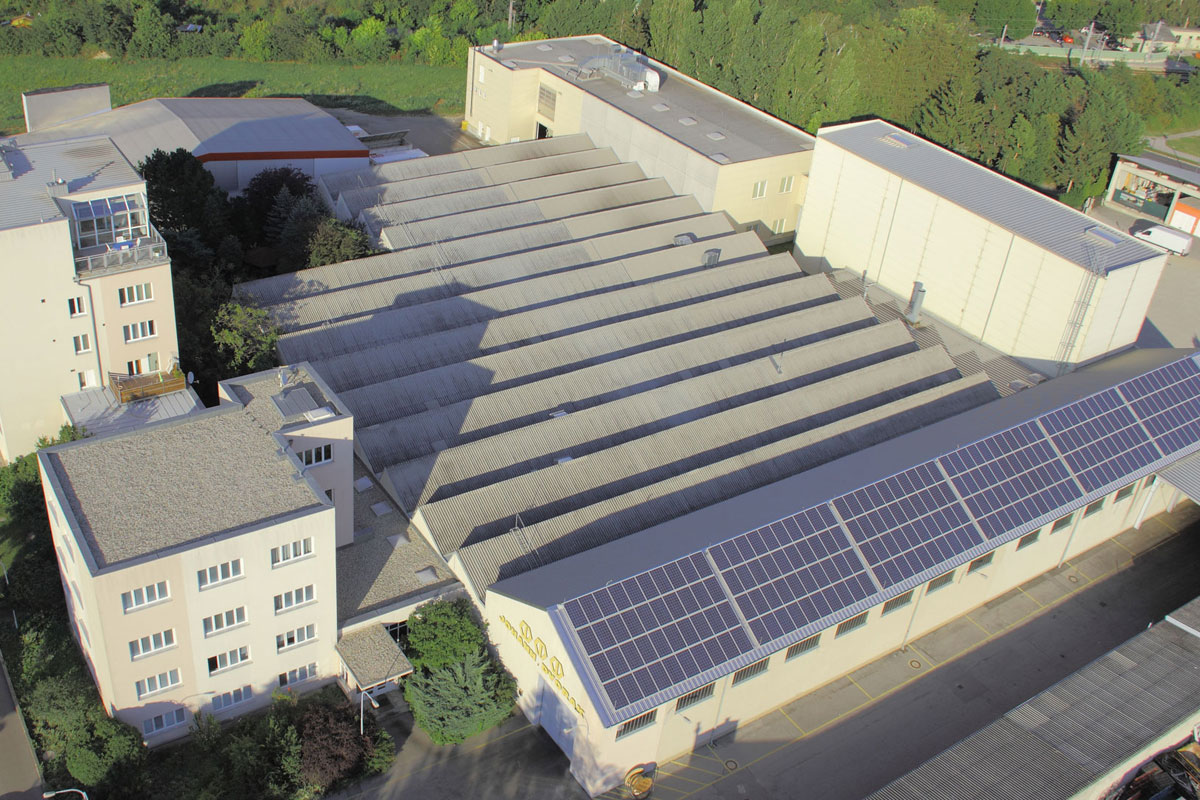
1975
Foundation of the sales company METUSAN Metallwarenhandelsgesellschaft m. b. H.
Expansion of the property area to 17 000 m²
Production area: 5 000 m²
1992
Restructuring of the group: Mr. Ing. Johann Dvorak, born 1967 founded the Johann Dvorak Produktions-G.m.b.H.
Sales: > 100 Mio ATS ( 7,3 Mio. €)
Export: > 70%
Machinery: ca. 100 cam single- and multispindle turning machines
1995
Certification according to DIN 9001: EN 2001
1996
Restructuring of production
New construction of a production hall
General renovation of the remaining production halls
With a material input of approx. 3 000 t brass and 150 t copper pipes, the DVORAK Group is one of the most efficient companies in this area in Europe
1998
Commissioning of a fully automated high-bay warehouse (35 m long x 9 m deep x 16 m high) with approx. 1 500 pallet spaces
Contact
METUSAN TURNING GmbH
Wienerfeldstraße 6, 2120 Wolkersdorf
Phone: +43 (0) 2245 3181 0
Fax: +43 (0) 2245 3181 34
office@metusan.at
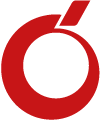
2000
Commissioning of a state-of-the-art, fully automated cleaning system
Investment in an additional chip processing system with a daily capacity of 10 000 kg of brass chips
2004
Commissioning of a semi-automatic packaging line
2005
Expansion of the machine park by 10 CNC-controlled automatic lathes
State award for applying the ‘Austrian Coat of Arms’
2006
Expansion of the machine park by 4 machining centers with robotic equipment
100th company anniversary
2007
Construction of an additional production hall.
This extends the production area from 6000 m² to 7600 m².
2008
Largest single investment in the company’s history in 4 CNC six-spindle automatic lathes
2009
Further expansion of the production capacity through additional 3 CNC six-spindle automatic lathes and a new shelving system in the raw material warehouse
2010
Implementation of two CNC 8-spindle automatic lathes for diameters up to 67 mm
2011
Expansion of the machine park with 2 CNC Gildemeister Sprint 65 single-spindle automatic lathes up to D 120 mm
To expand the idea of environmental protection, a more energy-efficient extraction system with oil separator was installed in the production hall
2012
Capacity expansion by purchasing another CNC Gildemeister Sprint 65 single-spindle automatic lathe
METUSAN turns green – participation in a 3.5 MW biomass cogeneration plant.
As of September 2012, METUSAN’s entire hot water and heating energy generation can be supplied by biomass.
This also includes the power supply via a photovoltaic system with 60kWp.
Contact
METUSAN TURNING GmbH
Wienerfeldstraße 6, 2120 Wolkersdorf
Phone: +43 (0) 2245 3181 0
Fax: +43 (0) 2245 3181 34
office@metusan.at
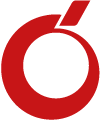
2013
Expansion of the production by investing in a CNC Gildemeister Sprint 65 for highly complex turned parts up to a diameter of 120 mm
Investment in two additional ZPS CNC 6-spindle automatic lathes for 42 mm diameter
2014
Hall expension of 400m² for tool making
Commissioning of the 5th CNC Gildemeister Sprint 65 automatic lathe
Expansion of the PV system by 400 m²
Participation in Weinviertler Mechatronik Akademie
2015
Commissioning of a CNC BML-Smart pipe bending machine for brass and copper pipes from 6 – 28 mm
New department for brazing of brass and copper assemblies
2016
METUSAN was one of the first Austrian companies to be certified according to the new quality standard ISO 9001: 2015
Investment in two CNC 8-spindle automatic lathes
2017
Investment in 4 CNC Maier double spindle machines
Obtaining the ISO 14001: 2015 environmental management certificate
2018
Construction of production hall 5 with 1 870 m²
Completion of the shell construction of the office building with 960 m²
2019
Relocation of the CNC single-spindle automatic lathes in production hall 5
Investment in 2 new high-precision washing systems
Investment in a cam 6-spindle automatic lathe (newer design)
Expansion of the PV system by 400 m²
2020
Investment in 8 new CNC single-spindle automatic lathes
Investment in 2 revitalized curves 6-spindle automatic lathes
2021
Investment in hardness testing machine and calibration machine
Investment in 3 revitalized curves 6-spindle automatic lathes
Investment in a cam 6-spindle automatic lathe (newer design)
Investment in 2 CNC mulit-spindle automatic lathes
Investment in 6 new CNC single-spindle automatic lathes
Investment in 1 CNC milling center with 5 axis
Implementation of an MDE system (machine data collection)
2022
Investment in 1 chip centrifuge
Investment in 1 CNC cylindrical grinding machine
Investment in 3 revitalized curves 6-spindle automatic lathes
Investment in 1 CNC turning/milling center
Investment in 2 new CNC single-spindle automatic lathes
Investment in 2 CNC mulit-spindle automatic lathes
2023
Investment and Acqusition in the German machining company Carl Leipold GmbH.
Through the combined strengths, this partnership will be further developed under the brand “THE TURNING PARTNER”.
THE TURNING PARTNER opens an extensive product portfolio.
Investment in 4 single-spindle automatic lathes Emco
Investment in 1 single-spindle automatic lathes Ergomat
Investment in 3 single-spindle automatic lathes Index ABC
Investment in 3 mulit-spindle automatic lathes DMG
Investment in 1 mulit-spindle automatic lathes Index MS32-6